Po dłuższej przerwie wracam z kolejną dawką wiedzy z zakresu sterowania napędami elektrycznymi. Tym razem przybliżę Wam temat pomiaru prędkości obrotowej (położenia) wału silnika i skutków awarii odpowiedzialnego za to czujnika.
Jak już wcześniej ustaliliśmy, precyzyjne sterowanie napędami elektrycznymi wymaga stosowania skomplikowanych metod, w których niezbędna jest znajomość wartości podstawowych zmiennych stanu maszyny. Możecie sobie o tym doczytać w moich poprzednich wpisach: Część I: algorytmy sterowania i Część II: przemienniki częstotliwości. Trudno mierzalne wielkości, na ogół, uzyskuje się poprzez estymację.
Natomiast niektóre zmienne, niezbędne do działania układów sterowania wektorowego, tj. prędkość obrotowa, napięcie i prąd stojana, mogą być bez większych trudności mierzone za pomocą czujników pomiarowych [1], [2]. Dokładny pomiar aktualnej wartości prędkości wału mechanicznego maszyny odgrywa bardzo ważną rolę jako jeden z głównych sygnałów sprzężenia zwrotnego w zaawansowanych strukturach sterowania [3]. Pomiar wartości prędkości obrotowej może być realizowany przez dedykowane do tego celu czujniki, które można podzielić na dwie główne kategorie [3]:
- bezpośrednio przetwarzające prędkość obrotową na sygnał elektryczny (np. prądnica tachometryczna),
- wyznaczające prędkość obrotową poprzez różniczkowanie kąta obrotu (przetworniki obrotowo-impulsowe z wyjściem cyfrowym lub analogowym, przetworniki kodowe oraz resolwery).
Enkodery obrotowo-impulsowe
Jednymi z najczęściej stosowanych czujników pomiarowych wielkości mechanicznych spotykanych w aplikacjach przemysłowych są przetworniki optoelektroniczne nazywane enkoderami [4]. Zamieniają one ruch obrotowy elementów wirujących na sygnały pozwalające określić ich położenie kątowe, ilość obrotów, kierunek obrotu i prędkość obrotową.
Przetworniki optoelektroniczne można podzielić, ze względu na pełnione funkcje, na dwa rodzaje:
- obrotowo-impulsowe,
- obrotowo-kodowe [5].
Pierwsze z nich mają możliwość rozpoznawania kierunku obrotu i odległości względnej. Główną różnicą między tymi czujnikami jest rodzaj sygnału wyjściowego oraz możliwość pamiętania mierzonej wielkości.
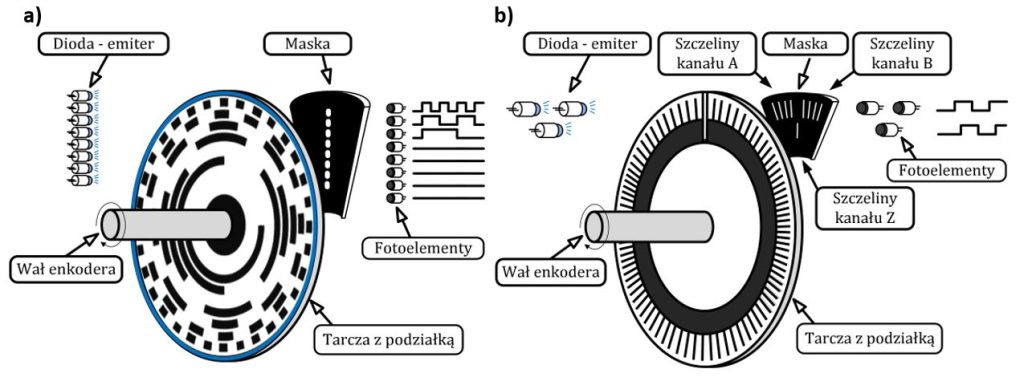
Enkodery absolutne
Enkoder absolutny (Ryc. 1a) generuje sygnał kodowy binarny lub Gray’a [6]. Na Ryc. 2b przedstawiłem przykładową tarczę enkodera absolutnego, a na Ryc. 2c i 2d tarcze dla obu typów kodowania 4-bitowego.
Każdemu położeniu kątowemu wału mechanicznego odpowiada konkretna wartość kodowa na wyjściu. Można rozróżnić enkodery absolutne:
- jednoobrotowe – odczytujące pozycję tylko w zakresie jednego obrotu,
- wieloobrotowe – informujące zarówno o pozycji kątowej jak również o liczbie wykonanych obrotów.
Istotną cechą enkodera absolutnego jest znacznie większa niż w przypadku innych czujników liczba par diod emiter – odbiornik [6].
Charakterystyczną własnością przetwornika jest jego zdolność do pamiętania aktualnej pozycji nawet po wyłączeniu napięcia zasilającego układ, co wynika bezpośrednio z budowy tarczy pomiarowej. Rozdzielczość enkodera określana jest za pośrednictwem ilości bitów w jakich przedstawiany jest wynik [6].
Enkodery inkrementalne
W enkoderze inkrementalnym (Ryc. 1b) sygnałem wyjściowym są impulsy zero-jedynkowe generowane przez układ optyczny. Składa się on z emitera, odbiornika (fotoelementów) oraz obracającej się między nimi tarczy [4], [7]. Na niej umieszczone są w równych odległościach od siebie przezroczyste prążki, przepuszczające cyklicznie światło ze źródła do odbiornika, które poddawane jest cyfrowej obróbce przez układ elektroniczny.
Na Ryc. 2a przedstawiłem przykładową tarczę stosowaną w enkoderach inkrementalnych.
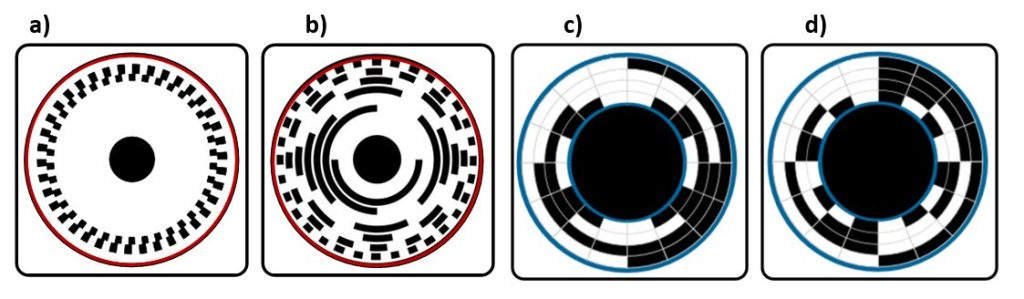
Rozdzielczość przetwornika określa się jako ilość impulsów generowanych na jeden obrót tarczy enkodera. Im jest ona większa, tym mniejsze przesunięcia kątowe można zmierzyć. Istotnym aspektem czujnika jest poprawne określenie kierunku obrotu wału mechanicznego silnika. W praktycznych zastosowaniach wykorzystuje się dwie pary układu emiter – odbiornik, które są przesunięte względem siebie o kąt 90°, co pozwala na jednoznaczne rozróżnienie kierunku obrotu wału enkodera przez rozpoznanie, na którym kanale (A czy B) pojawia się jako pierwszy sygnał prostokątny w jednym cyklu pracy (Ryc. 3).
Możliwe jest także uzyskanie informacji o wykonaniu pełnego obrotu wału mechanicznego poprzez dodanie kanału zerowego w postaci pojedynczego prążka na masce enkodera. W efekcie na wyjście czujnika wysyłany jest sygnał prostokątny adekwatny do przesunięcia kątowego wału. Konstrukcja enkodera inkrementalnego nie pozwala zapamiętać aktualnego położenia tarczy przetwornika.

Problemy eksploatacyjne enkoderów
Jednym z głównych problemów dotyczących eksploatacji enkoderów w trudnych warunkach otoczenia, jest wnikanie wody i zanieczyszczeń do środka urządzenia. Poprawne działanie tych przetworników jest silnie uzależnione od stopnia czystości w obrębie obudowy, z tego względu, że wszelkie zabrudzenia przenikające do wnętrza czujnika skutkują błędami pomiaru [8].
Drugim ważnym czynnikiem jest mechaniczna wytrzymałość tych czujników. Negatywnym zjawiskiem, powodującym zbyt duże obciążenie enkodera, jest brak współosiowości wału przetwornika i maszyny, do której enkoder jest zamocowany. Pod wpływem powstających wibracji tarcza może zostać zarysowana lub całkowicie uszkodzona [8].
Enkodery magnetyczne i pojemnościowe
Problemy związane z wpływem zanieczyszczeń na dokładność pomiaru praktycznie nie dotyczą enkoderów magnetycznych i pojemnościowych. Przetworniki tego rodzaju charakteryzuje mniejsza wrażliwość na wibracje i uderzenia oraz dużo większa odporność na uszkodzenia mechaniczne [9].
Enkodery magnetyczne
W enkoderach magnetycznych absolutnych występują dwa zasadnicze elementy:
- wirująca tarcza z naniesionym magnetycznie kodem,
- czujnik mierzący zmiany pola magnetycznego. Stosowane są głównie dwa rodzaje takich przetworników: czujniki Halla oraz czujniki magnetorezystywne [9], [10].
W nowoczesnych pojazdach czujniki Halla mają wiele różnorodnych zastosowań. W jednostce napędowej urządzenia tego typu pełnią funkcję pomiarową, dzięki czemu określane jest położenie i prędkość obrotowa wałka rozrządu i wału korbowego. W układach ABS czujnik Halla wykorzystywany jest do pomiaru prędkości obrotowej kół. Dzięki temu urządzenie jest w stanie wychwycić moment zablokowania koła podczas hamowania i wysyła sygnał do jednostki sterującej układem ABS [11].
Czujniki magnetorezystywne mają nieliniową charakterystykę z histerezą oraz są wrażliwe na zewnętrzne pole magnetyczne. Ponadto, nie posiadają one możliwości wyznaczania bezwzględnej pozycji w ramach jednego obrotu wału maszyny wirującej. Czujniki Halla nie mają tych wad, a pomiar różnicowy z kilku czujników Halla pozwala zredukować wpływ zewnętrznego pola magnetycznego na poprawność wyników.
Z tego względu, na ogół, czujniki Halla są stosowane w enkoderach magnetycznych [9], [12]. Napięciowy sygnał wyjściowy z przetwornika jest przetwarzany do postaci kodu cyfrowego odzwierciedlającego pozycję tarczy, tak jak w klasycznym czujniku optycznym.
Zalety i wady przetworników magnetycznych
Głównymi zaletami przetworników magnetycznych są:
- duży zakres temperatur pracy (od minusowych temperatur do przekraczających 100°C),
- możliwość odseparowania elementów elektronicznych i pomiarowych od części mechanicznej,
- pomiar przemieszczenia absolutnego i przyrostowego.
Główną wadą tych enkoderów jest mniejsza w porównaniu do przetworników optycznych rozdzielczość [9], [12]. O ile rozwiązanie tego typu zapewnia dłuższą żywotność, enkoder magnetyczny zazwyczaj nie jest tak dokładny, jak enkoder optyczny, a niektóre rodzaje są również wrażliwe na interferencje elektromagnetyczne powodowane przez sam silnik.
Czujniki pojemnościowe
Czujniki pojemnościowe łączą zalety enkoderów optycznych oraz magnetycznych. Przetwornik w klasycznej postaci składa się z dwóch płytek: jednej nieruchomej, a drugiej połączonej z wałem obrotowym (Ryc. 4). Dwa rzędy podziałek lub linii, jeden na nieruchomym, a drugi na ruchomym elemencie, tworzą kondensator o zmiennej pojemności.
Zasada działania enkoderów pojemnościowych opiera się na zmianie pojemności, która odpowiada położeniu elementu obrotowego. Przetworniki tego typu są wykonywane jako dwu– lub trzyczęściowe [8]. W trzyczęściowym czujniku pole elektryczne między nieruchomymi okładkami kondensatora jest zaburzane przez poruszający się element z dielektryka. Natomiast w przetworniku drugiego typu jedna płytka jest nieruchoma, a druga jest połączona z obrotowym wałkiem. Wraz z obrotami enkodera wewnętrzny układ scalony zlicza zmiany i dokonuje interpolacji, aby określić pozycję wału i kierunek obrotu [8].
W ten sposób otrzymuje się standardowe wyniki kwadraturowe oraz fazy komutacji używane do sterowania silnikami BLDC [8].
![Ryc. 4 Konstrukcja enkodera pojemnościowego [12] Konstrukcja enkodera pojemnościowego](https://sii.pl/blog/wp-content/uploads/2024/01/napedy-elektryczne_4.jpg)
Zalety czujników pojemnościowych
Do zalet technologii pojemnościowej należy odporność na zanieczyszczenia, takie jak piach, pył i olej oraz brak elementów, które ulegałyby zużyciu, takich jak diody (LED) [8]. Dzięki temu układy są bardziej niezawodne od modeli optycznych. W obu przypadkach na podstawie zmian pojemności generowany jest sygnał elektryczny, który po odpowiednim przetworzeniu niesie informację o absolutnym przemieszczeniu obrotowego elementu. Duża dokładność oraz niezawodność sprawiają, że przetworniki pojemnościowe są stosowane coraz częściej w elektronicznych układach sterowania w pojazdach [8].
Wpływ uszkodzeń enkodera na pracę napędu elektrycznego
Przejdźmy teraz do drugiej części tytułu artykułu i poruszmy temat awaryjności opisanych czujników.
Skutki uszkodzeń we wszystkich przypadkach będą miały zbliżony wpływ na pracę napędu, dlatego skupię na jednym z prostszych przykładów – enkoderze inkrementalnym. Jedną z najczęstszych przyczyn awarii tych przetworników jest uszkodzenie obudowy, co powoduje przedostawanie się zanieczyszczeń do ich wnętrza. Przyczynia się to do zaburzenia pracy układu emiter-odbiornik, wpływając negatywnie na jakość pomiaru przesunięcia kątowego.
Przyczyny uszkodzeń przetworników optycznych
Kluczowym elementem enkodera inkrementalnego jest tarcza z podziałką, na której prążki są rozłożone w równych odstępach od siebie oraz w odpowiedniej odległości od źródła i odbiornika światła (poniżej 0,5 mm). Silne wstrząsy oraz drgania mechaniczne mogą powodować przesunięcie tarczy bądź też jej zniszczenie. Temperatura otoczenia, która przekracza dopuszczalny przez producenta zakres, oraz zewnętrzne zaburzenia elektromagnetyczne mogą także doprowadzić do zakłócenia pracy elementów elektronicznych, półprzewodnikowych czy też uszkodzenia przewodów łączeniowych znajdujących się wewnątrz układu pomiarowego.
Wymienione powyżej uszkodzenia przetworników optycznych negatywnie wpływają na pracę napędu elektrycznego. Skutki awarii przetworników pomiarowych mogą przybierać różną formę, w zależności od jej rodzaju.
Najbardziej prawdopodobne uszkodzenia enkodera inkrementalnego przedstawiono na Ryc. 5.
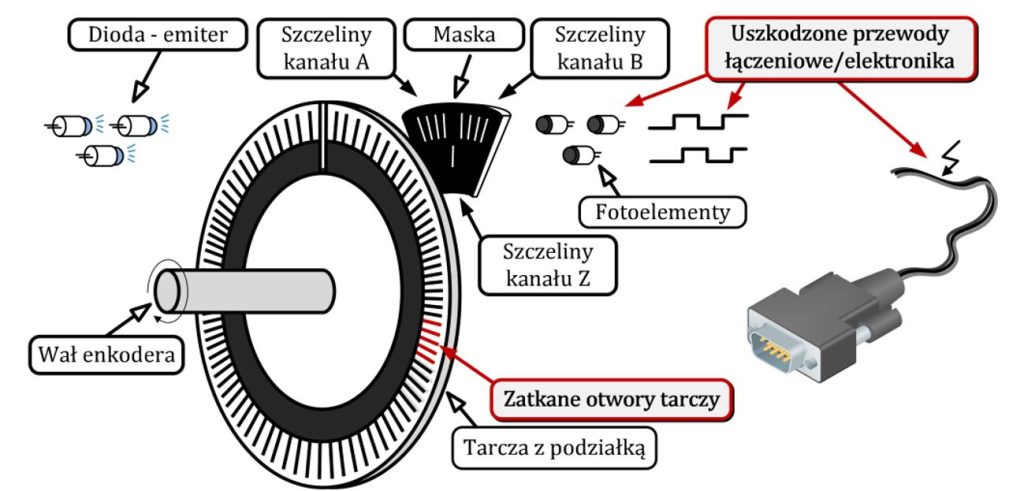
Uszkodzenia enkodera
Awarie te można zdefiniować prostą zależnością [13]:
\[\omega_m^{enk}=\left(1-\gamma\right)\omega_m\]
gdzie:
$\omega_m^{enk}$ – mierzona wartość prędkości mechanicznej,
$\omega_m$ – rzeczywista wartość prędkości mechanicznej,
$\gamma$ – współczynnik pomocniczy, przy czym: -1 ≤ $\gamma$ ≤ 1.
W zależności od współczynnika γ, otrzymywana wartość prędkości mechanicznej z czujnika może być:
- przerywana – ograniczenie liczby impulsów spowodowane blokowaniem otworów tarczy enkodera, -1 < $\gamma$ < 1;
- cyklicznie przerywana – uszkodzenie elektroniki lub przewodów zasilających, $\gamma$ = [0,1];
- zerowa – całkowite przerwanie pętli pomiarowej, $\gamma$ = 1;
Na Ryc. 6-9 przedstawiono przebiegi:
- prędkości kątowej,
- strumienia wirnika,
- składowych prądu stojana isx i isy,
- momentu elektromagnetycznego,
- prądu stojana isA, isB,
podczas awarii czujnika prędkości w strukturze sterowania polowo zorientowanego DRFOC, która została przedstawiona w moim pierwszym artykule na blogu.
Dodatkowo w układzie wykorzystywany jest estymator prędkości kątowej w celu porównania prędkości estymowanej z wartością rzeczywistą oraz estymator strumienia wirnika.
W chwili t=0 s przeprowadzono rozruch silnika do prędkości znamionowej. Dla t=0,25 s, t=1,1 s, t=1,5 s obciążano silnik znamionowym momentem obciążenia. Wyraźnie widoczne jest, że napęd pracuje w sposób prawidłowy. Strumień wirnika utrzymywany jest na stałej (znamionowej) wartości, a moment elektromagnetyczny zmienia się zgodnie ze zmianami prędkości i obciążenia. Uszkodzenie enkodera następuje w chwili t=1s.
Konsekwencje zaniku sygnału z czujnika
Nagły zanik sygnału z czujnika (podpunkt (a) z Ryc. 6-9) spowodował nagły wzrost prędkości kątowej silnika oraz momentu elektromagnetycznego proporcjonalnego do składowej isy prądu stojana.
Wynika to z faktu, że regulator prędkości wystawia na wyjściu maksymalną dopuszczalną wartość, reagując na nagle zwiększający się uchyb pomiędzy wartością referencyjną prędkości a mierzoną, co powoduje, że zadana składowa prądu isyref ustala się na stałym poziomie. Zakłóceniu ulegają również przebiegi składowej isx oraz modułu strumienia wirnika, ale w znikomym stopniu.
![Ryc. 6 Przebiegi prędkości mierzonej, rzeczywistej oraz estymowanej przy wystąpieniu uszkodzenia czujnika prędkości: (a) – uszkodzenie całkowite (γ = 1), (b) – uszkodzenie elektroniki (γ = [0,1]), (c) – uszkodzenie tarczy enkodera (-1 < γ < 1), od chwili t=1s, wyniki symulacyjne, sterowanie DRFOC, ωm = ωmN,mo=moN Przebiegi prędkości mierzonej, rzeczywistej oraz estymowanej przy wystąpieniu uszkodzenia czujnika prędkości](https://sii.pl/blog/wp-content/uploads/2024/01/napedy-elektryczne_6.jpg)
![Ryc. 7 Przebiegi składowych isx i isy prądu stojana przy wystąpieniu uszkodzenia czujnika prędkości: (a) – uszkodzenie całkowite (γ = 1), (b) – uszkodzenie elektroniki (γ = [0,1]), (c) – uszkodzenie tarczy enkodera(-1 < γ < 1), od chwili t=1s, wyniki symulacyjne, sterowanie DRFOC, ωm = ωmN,mo=moN Przebiegi składowych isx i isy prądu stojana przy wystąpieniu uszkodzenia czujnika prędkości:](https://sii.pl/blog/wp-content/uploads/2024/01/napedy-elektryczne_7-1024x321.jpg)
(-1 < γ < 1), od chwili t=1s, wyniki symulacyjne, sterowanie DRFOC, ωm = ωmN,mo=moN
![Ryc. 8 Przebiegi estymowanego modułu strumienia wirnika i momentu elektromagnetycznego przy wystąpieniu uszkodzenia czujnika prędkości: (a) – uszkodzenie całkowite (γ = 1), (b) – uszkodzenie elektroniki (γ = [0,1]), (c) – uszkodzenie tarczy enkodera (-1 < γ < 1), od chwili t=1s, wyniki symulacyjne, sterowanie DRFOC, ωm = ωmN,mo=moN Przebiegi estymowanego modułu strumienia wirnika i momentu elektromagnetycznego przy wystąpieniu uszkodzenia czujnika prędkości](https://sii.pl/blog/wp-content/uploads/2024/01/napedy-elektryczne_8-1024x314.jpg)
![Ryc. 9 Przebiegi prądów fazowych isA i isB przy wystąpieniu uszkodzenia czujnika prędkości: (a) – uszkodzenie całkowite (γ = 1), (b) – uszkodzenie elektroniki (γ = [0,1]), (c) – uszkodzenie tarczy enkodera (-1 < γ < 1), od chwili t=1s, wyniki symulacyjne, sterowanie DRFOC, ωm = ωmN,mo=moN Przebiegi prądów fazowych isA i isB przy wystąpieniu uszkodzenia czujnika prędkości](https://sii.pl/blog/wp-content/uploads/2024/01/napedy-elektryczne_9-1024x327.jpg)
W chwilach obciążenia silnika momentem znamionowym zmniejsza się wartość rzeczywistej prędkości kątowej silnika. Moment elektromagnetyczny wzrasta odpowiednio do obciążenia. Wartości zadane składowych isyref pozostają bez zmian i utrzymują się na maksymalnym poziomie, zatem utraciliśmy zdolność do sterowania układem. Adekwatnie do momentu elektromagnetycznego reagują także składowe prądu stojana.
Bez wątpienia całkowite przerwanie pętli pomiarowej z enkodera ($\gamma$=1) jest najgroźniejszym typem awarii, jaki może się wydarzyć i z punktu widzenia sterowania napędem niesie ze sobą katastrofalne skutki.
Konsekwencje awarii elektroniki enkodera
Kolejne wyniki przedstawione w podpunktach (b) i (c) z Ryc. 6-9 dotyczą uszkodzeń, które objawiają się pobieraniem przerywanego sygnału z czujnika. Może być to spowodowane awarią elektroniki enkodera, przewodów łączących i zasilających fotoelement (podpunkty (b)) lub uszkodzeniem (zablokowaniem otworów) tarczy enkodera (podpunkty (c)).
Należy tutaj pamiętać, że w zależności od typu silnika, metody sterowania, rodzaju czujnika, jego budowy, rozdzielczości i zasady działania, przebieg zakłócenia może przybierać nieco inną formę, jednakże wpływ uszkodzenia powinien być zbliżony do przedstawionego. Dodatkowo, przy tych awariach, skutki będą tym dotkliwsze i bardziej znaczące dla pracy napędu, im większy stopień zaawansowania uszkodzenia nastąpi.
Wracając do przykładu enkodera, awaria jego elementów elektronicznych wpływa negatywnie na przebiegi prędkości kątowej, momentu elektromagnetycznego i w znikomym stopniu na przebieg modułu strumienia (podpunkty (b)).
Spowodowane jest to cyklicznymi zanikami sygnału pomiarowego z enkodera, które skutkują wymuszeniem dużych chwilowych wartości prądu stojana. W przebiegach odtwarzanego momentu elektromagnetycznego zauważalne są silne oscylacje wynikające z cyklicznego wystawiania przez regulator prędkości maksymalnych (bądź bliskich maksymalnych) wartości zadanej składowej isyref prądu stojana.
Moduł strumienia wirnika i składowa isx prądu stojana w strukturze sterowania polowo zorientowanego nie reagują w tak istotnym stopniu jak pozostałe zmienne stanu, a obciążenie silnika momentem znamionowym zdaje się minimalnie zmniejszać wpływ uszkodzenia na pracę napędu.
Konsekwencje zablokowania otworów tarczy enkodera
Skutki zablokowania otworów tarczy enkodera przedstawiono na podpunktach (c) tych samych rysunków. Gubienie pojedynczych impulsów sygnału pomiarowego przy pełnym obrocie tarczy enkodera nie powoduje znaczących negatywnych skutków w pracy napędu. Wynika to z faktu, że stałe czasowe układu regulacji prędkości kątowej są większe, niż czas trwania impulsu generowanego przy wystąpieniu awarii.
Niemniej jednak, zauważalne są silne oscylacje estymowanego momentu elektromagnetycznego i mierzonych prądów fazowych silnika. Również ten typ uszkodzenia może spowodować dużo poważniejsze konsekwencje, jeżeli nie zostanie wyeliminowany dostatecznie szybko.
Zablokowanie otworów tarczy wynika z utraty szczelności czujnika, zatem po wystąpieniu takich przebiegów należy się spodziewać eskalacji awarii i jej coraz bardziej znaczącego wpływu na skuteczność sterowania i w konsekwencji pracę silnika.
Podsumowanie
Wyraźnie widoczne jest, że każdy rodzaj uszkodzenia czujnika prędkości wpływa niekorzystnie na pracę napędu sterowanego metodą wektorową. Najgorsze w skutkach jest całkowite przerwanie pętli pomiarowej. Cykliczne gubienie impulsów oraz zanik impulsów z enkodera nie powoduje utraty stabilności napędu, jednak długotrwała praca w takim stanie może doprowadzić do uszkodzenia silnika lub elementów energoelektroniki (np. falownika). W zależności od stopnia zaawansowania tych awarii, skutki mogą mieć łagodniejszy lub silniejszy wpływ na pracę napędu.
Wspominałem wcześniej o estymatorach wielkości trudno mierzalnych (strumień i moment). Układy te bazują na dostępnych sygnałach sterujących i pomiarowych, w tym oczywiście prędkości kątowej i prądach stojana. W zależności od rodzaju użytego estymatora skutki uszkodzeń również mogą być dużo gorsze lub przebiegać w nieco inny, ale nadal niekontrolowany sposób.
Kolejnym czynnikiem, który ma wpływ na przebieg awarii jest samo sterowanie. Przedstawiłem wyniki symulacyjne zostały przeprowadzone z dużą dokładnością (niskim krokiem całkowania). W praktycznych aplikacjach zarówno tory sterowania jak i pomiarowe mogą funkcjonować z różnymi i/lub większymi krokami obliczeń, co spowoduje bardziej skokowe i opóźnione próby opanowania awarii, a w konsekwencji jeszcze groźniejsze stany nieustalone.
Oczywiście istnieją już systemy, które są w stanie skutecznie odizolować uszkodzenie w celu zapewnienia bezpieczeństwa systemu oraz użytkownika. Jednakże w większości przypadków powodują one awaryjne wyłączenie układu, zwłaszcza, jeżeli nie jest możliwa dalsza stabilna praca napędu.
***
W następnych artykułach na blogu przedstawię metody detekcji awarii, które pozwolą na skuteczne odizolowanie tylko wadliwych urządzeń pomiarowych i dalszą bezpieczną pracę napędu. Takie układy sterowania nazywane są w literaturze systemami odpornymi na uszkodzenia FTC (ang. Fault Tolerant Control). Ale najpierw opowiem o uszkodzeniach czujników pomiarowych wielkości elektrycznych, które pełnią równie ważną, bądź nawet ważniejszą, rolę.
Literatura
Część teoretyczna została opracowana na podstawie poniższych pozycji literatury:
[1] Dybkowski M., Estymacja prędkości kątowej w złożonych układach napędowych – zagadnienia wybrane, Prace Naukowe Instytutu Maszyn, Napędów i Pomiarów Elektrycznych Politechniki Wrocławskiej, Monografie, vol. 67, nr 20, 2013
[2] Orłowska-Kowalska, T., Bezczujnikowe układy napędowe z silnikami Indukcyjnymi, Oficyna Wydawnicza Politechniki Wrocławskiej, Wrocław 2003
[3] Niewiatowski J., Algorytm tachometru, Pomiary Automatyka Robotyka, nr 16, str. 73-78, 2012
[4] Incze I., Negrea A., Imecs M., Szabó C., Incremental encoder based position and speed identification: modeling and simulation, Acta Universitatis Sapientiae, Series Electrical and Mechanical Engineering, nr 2, str. 27-39, 2010
[5] Brock S., Zawirski K., Cyfrowy pomiar prędkości obrotowej w napędzie elektrycznym, Pomiary Automatyka Robotyka, vol. 8, nr 1, str. 10-13, 2005
[6] Krąpczyński K., Enkodery absolutne. Pomiary Automatyka Robotyka, nr 6, str. 16-17, 2002
[7] Petrella R., Tursini M., Peretti L., Zigliotto M., Speed measurement algorithms for low resolution incremental encoder equipped drives: a comparative analysis, International Aegean Conference on Electrical Machines and Power Electronics, ACEMP ’07, str. 780-787, 2007
[8] Przetworniki kąta obrotu – kompedium, Automatykab2b.pl, 2017. [Online]
[9] Nowakowski W., Czujniki Indukcyjne w automatyce, część 1. Elektronika Praktyczna nr. 4, 2006
[10] Chaleba A., Poniński M., Siedlecki A., Metrologia elektryczna, WNT, 1998
[11] Intercars, Blog internetowy [Online]
[12] Belous A., Saladukha V. (2020). Basic Components of Telecommunication Systems. In: High-Speed Digital System Design. Springer, Cham
[13] Lee K. S., Ryu J., Instrument fault detection and compensation scheme for direct torque controlled Ind.uction motor drives, IEE Control Theory Applications, vol. 150, nr 4, str. 376–382, 2003
Zostaw komentarz